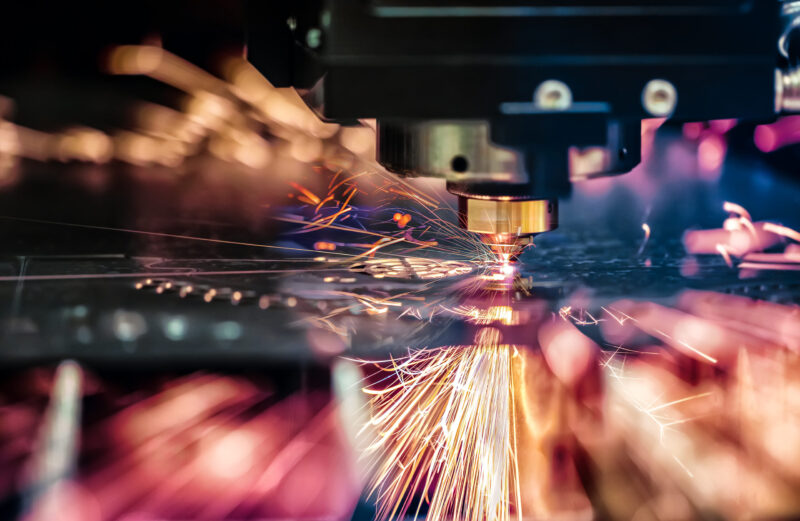
This site
is mobile
responsive
The Malaysian iron and steel industry faces the vital need to decarbonise its operations. In the global transition to a low-carbon economy, the industry must adapt, minimise its carbon footprint and ensure its sustainability for long-term growth. Globally, the iron and steel industry contributes nearly 40% of industrial emissions, putting the industry under intense pressure to transition towards sustainability. Recognising this, the Malaysian Government has prioritised the decarbonisation of the iron and steel industry under the New Industrial Master Plan (NIMP) 2030. This strategic initiative aims to align industrial growth with the nation’s commitment to achieving net-zero emissions by 2050.
1. High Investment Cost
Decarbonising the iron and steel industry requires high investment costs due to the extensive modifications needed in current production processes. Upgrading existing infrastructure, implementing new technologies and developing alternative energy sources all contribute to the high expenses involved in transitioning to a more sustainable production model. Key factors contributing to the high investment costs include:
2. Maintaining steel quality
The shift towards decarbonised steel production introduces challenges in maintaining consistent product quality. Transitioning from traditional coal-based processes, such as the blast furnace-basic oxygen furnace (BF-BOF), introduces variables that may disrupt production flow and potentially affect steel’s chemical composition and mechanical properties. Integrating innovative technologies like hydrogen-based production or CCUS requires significant production process adjustments, potentially impacting consistency. Ensuring high-quality standards is critical for the steel industry’s competitiveness and success in a low-carbon future.
In addition to the global hurdles, Malaysia faces some distinct challenges in its decarbonisation pathway:
1. Raw Material Availability
The limited domestic availability of high-grade steel scrap presents a significant obstacle to Malaysia’s decarbonisation goals in the steel sector. Decarbonisation strategies often centre around EAF technology, which relies heavily on a consistent supply of high-quality metal scrap as a primary raw material. Malaysia’s dependence on imported metal scrap exposes the industry to price volatility and potential supply chain disruptions, hindering its transition to a sustainable and competitive steelmaking sector.
2. Workforce Upskilling
The transition to low-carbon steel production requires a workforce equipped with specialised skills in areas like carbon accounting, green certification and energy management. Developing a talent pool in these areas is crucial for successful decarbonisation.
Despite the challenges, the NIMP 2030 lays out a comprehensive roadmap for transforming Malaysia’s iron and steel industry into a globally competitive and sustainable sector. This policy provides significant opportunity for the growth of Malaysia’s iron and steel industry:
1. Policy Support
The NIMP 2030 promotes the importance of decarbonisation in the iron and steel industry by introducing a carbon footprint policy and measures to support the net-zero carbon agenda and circular economy. Initiatives such as mandatory carbon audits, reporting, and carbon taxes encourage environmental accountability. These measures position Malaysia’s iron and steel industry as an environmental leader, appealing to eco-conscious global markets and meeting Environmental, Social, and Governance (ESG) standards.
2. Shift to High-Value-Added Products
Rising global demand for high-grade steel and specialised metal products incentivises industry players to transition towards sustainable practices and high-value-added manufacturing. The policy encourages investments in advanced machinery and research and development (R&D) activities to enhance technological capabilities and production structures. Industry players are also urged to intensify research in advanced materials and collaborate with global partners to foster innovation, promote technology transfer and boost local capabilities. These initiatives will reduce reliance on imports and position Malaysia as a key supplier of high-quality steel, creating long-term resilience in the global value chain.
3. Market Advantage
As the world prioritises sustainability, demand for environmentally friendly products is growing rapidly. For steelmakers, transitioning to low-carbon production not only benefits the planet but also enhances competitiveness. Producing green steel allows companies to differentiate themselves in global markets like Europe and the United States, where environmental regulations are stricter. This approach also attracts customers and businesses that prefer eco-friendly suppliers. By focusing on greener products, steelmakers can tap into this growing demand and secure their place in a more sustainable future.
4. Funding and Investment Support
The introduction of targeted financing mechanisms, such as grants and incentives under the NIMP 2030, assumes a crucial role in empowering local steelmakers, especially Small and medium enterprises (SMEs), to advance low-carbon steelmaking solutions. For instance, the Domestic Investment Accelerator Fund (DIAF) offers matching grants specifically designed to help Malaysian-owned SMEs and Mid-Tier Companies (MTCs) in the manufacturing and selected services sectors to adopt ESG practices. This strategic support not only accelerates the transition to sustainable operations but also strengthens competitiveness in an increasingly ESG-focused global market.
Decarbonising Malaysia’s iron and steel industry demands a comprehensive strategy encompassing investments in advanced technologies, clean energy infrastructure, supportive policies, targeted innovation, and workforce upskilling.
Key initiatives include promoting CCUS technologies, incentivising the transition to EAF and hydrogen-based DRI technologies, and leveraging the upcoming carbon tax to accelerate the shift to greener steel production.
The Government’s commitment to developing a detailed decarbonisation pathway, in collaboration with industry associations and the Independent Steel Committee, will be crucial in guiding the industry towards a sustainable future.
To know more, please contact the Machinery and Metal Technology Division at https://www.mida.gov.my/staffdirectory/machinery-metal-technology-division/.