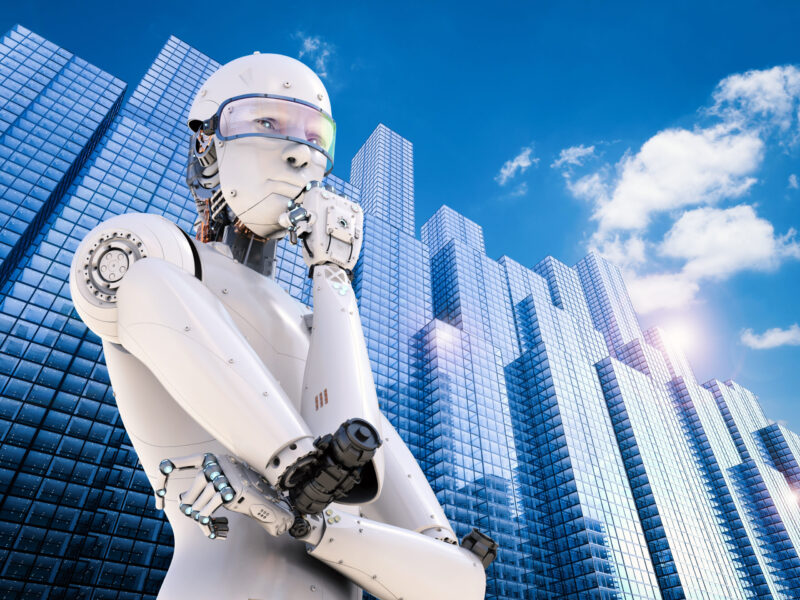
This site
is mobile
responsive
Additive Manufacturing (AM) is the process of building physical objects by layering materials like metal, plastic, or concrete using dedicated software and equipment.
AM, more widely known as 3D printing can be a force multiplier in the digital transformation of the manufacturing sector. AM produces components directly from a digital design file and prints the special raw material layer by layer to create specially-tailored material for producers.
As a result of its paradigm-shifting abilities that shorten both the design and manufacturing process of key components, AM technology is currently being explored extensively in the construction industry, otherwise called 3D Construction Printing (3DCP).
The embracement of AM among construction players also works well with the increased adoption of Industrialised Building System (IBS) modular construction, which puts together a building by fitting together preconstructed parts made in a factory. AM’s use thus can further shorten the IBS supply chain by autonomously manufacturing components directly from a digital design model with the least possible human intervention.
Given the construction sector’s high dependence on labour and impact on the environment, the use of AM and IBS work hand-in-hand to increase efficiency, reduce human errors, and improve construction sites’ carbon footprints.
These clear benefits have seen an uptake in demand in AM technologies worldwide, with the global AM to grow by some 23 percent annually between 2023 and 2025.
According to thyssenkrupp-IDC research, AM is expected to generate US$100 billion in economic value to Southeast Asian (ASEAN) nations by 2025. In 2019, the ASEAN bloc only accounts for five to seven per cent of Asia’s total AM expenditure at US$3.8 billion. Within ASEAN, demand for AM is led by construction-strong countries Singapore, Thailand, and Malaysia, which together make up 80 per cent of the ASEAN AM market.
In 2014, China-based company WinSun printed 10 single- storey detached houses in a day using four 33-foot wide and 22-foot tall concrete printers. Each house was printed for less than US$5,000 (RM20,950).
Two years later, the world’s first functional 3D-printed office opened in Dubai. The 2,700-square-foot structure was built in 17 days and cost US$140,000 (RM586,600) to print.
This was followed in 2018 with the first permitted 3D-printed home built in the US, a collaboration between US-based construction technology company ICON and non-profit organisation New Story. As part of their project to tackle homelessness in Austin, Texas, ICON printed a 350-square-foot house in 48 hours at a cost US$10,000 (RM41,900) as a proof of concept. Since then, the startup says it has delivered more than two dozen 3D-printed homes and structures across the U.S. and Mexico.
There are however, several major challenges in successfully marrying AM or 3DCP with IBS modular systems for large-scale construction projects. AM involves the additive assembly of only one material at a time, whereas houses are complex structures that comprise a wide range of material types.
In addition, the cost of building walls is currently much cheaper using conventional methods, especially in countries with relatively low labour costs, like Malaysia.
There are also some difficulties in converting homogeneous printing material used in the 1Dprinting process into a multidimensional 3D process.
The nascency of AM technology for construction purposes means machinery’s slow build rates affect efficiency of production. Some 3DCP printers lay down material at one to five cubic inches per hour. This can even be slower, depending on parts needed and manufacturing processes involved. Moreover, some 3DCP printers have poor mechanical properties, with the likelihood of layering and multiple interfaces causing product defects. Currently, there isn’t any manufacturer in AM for IBS in Malaysia.
However, the Construction Industry Development Board (CIDB), CIDB IBS, CIDB Construction Research Institute of Malaysia (CREAM) and KA Bina have collaborated to develop the first 3D printed home in ASEAN. The development of the mock-up unit commenced in December 2021 and is expected to be completed in the first quarter of 2022.
The Industry4WRD policy is a national policy which aims to transform the manufacturing sector and related services in Malaysia through 4IR applications and technologies from 2018 to 2025. AM has been designated as one of the 11 4IR Pillars outlined under this national strategy. Thus, all initiatives and incentives under Industry4WRD can be leveraged to promote and encourage the adoption and development of AM.
There are 18 different Centre of Excellence (COE)s in various universities across Malaysia, which drive industry–academia collaborations within each 4IR focus area. AM has the potential to be a featured industry in Malaysia’s upcoming New Industrial Master Plan.
This is in line with the five National Investment Aspirations (NIA): to increase economic complexity, create high-value jobs, extend domestic linkages, develop new and existing clusters, and improve inclusivity.
There are also multiple tax incentives and allowances to encourage higher adoption and production of AM software, machinery, and materials. Existing companies that want to adopt and integrate AM technologies into their business operations can explore Automation Capital Allowance, which is set at 200 per cent of expenditure incurred to purchase automation machinery or equipment used for the business.
Meanwhile, new R&D service providers that fulfil eligibility requirements can be considered for Pioneer Status (PS) or Investment Tax Allowance (ITA) under the R&D Incentive.
On the other hand, the IP Development Incentive caters for technology companies conducting R&D and have filed for patents, utility innovations or copyrighted software based on their R&D output. The incentive provides income tax exemption on the royalty or licensing fee revenues generated from those IPs.
For new manufacturing projects, companies can be considered for either PS or ITA for selected products under the Promoted List such as specialised machine tools or industrial machinery, modules for machinery or equipment and industrial parts or components, and selected AM materials that fall under the category of engineering plastic.
Reinvestment Allowance (RA) is available for existing companies which incur capital expenditure on expansion, diversification, automation or modernisation.
For the provision of technology solutions and software, the Digital Ecosystem Acceleration Scheme (DESAC) incentives announced under Budget 2022 is relevant to AM practitioners.
Under DESAC, new digital technology providers can be eligible for a corporate tax rate of 0 to 10 per cent for a maximum of 10 years.
Meanwhile, existing digital tech players undertaking diversification of new services or new segments may be eligible for a 10% corporate tax rate for up to 10 years. DESAC also covers ITA for digital infrastructure providers, of up to 100 per cent on qualifying capital expenditure incurred within a period up to 10 years.
For more information on investment incentives in AM and IBS construction, contact the Building Technology & Lifestyle Division of MIDA.
Source: MIDA e-Newsletter January 2022