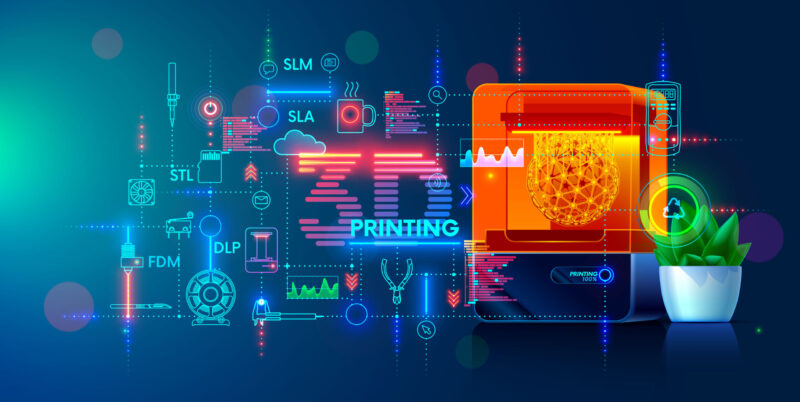
This site
is mobile
responsive
Additive manufacturing is a term coined by an industrialist who uses new approach in manufacturing industrial parts and components. Also known as 3D printing, both refers to the creation of lighter, robust parts and complex systems by depositing building materials layer upon layer in a successive cross section until the whole parts is complete. Additive manufacturing technology adds materials and melted it to create a line of superfine layer of an object which is difference with the conservative manufacturing. Conservative manufacturing, in order to produce parts will subtract materials via several processes such as milling, machining, grinding, carving etc.
Additive manufacturing has reached a tipping point globally where the development of materials, machine speeds and accuracy, and enabling software have combined to create a production-ready process. It is advancing from niche products to mainstream manufacturing. In-line with the government’s current policy in encouraging environmental, social and governance (ESG) best practices, industry players should also look at how additive manufacturing creates a more sustainable economy through several key advantages:
The findings by Frost and Sullivan suggested that the global value of the additive manufacturing is poised to grow at a compounded rate of 15.0% from US$5.31 billion in 2015 to US$21.50 billion in 2025. The aerospace, automotive and medical industries are expected to account for 51% of the 3D printing market by 2025. The growth in the additive manufacturing industry is predicted by many to be rapid and substantial, as more companies develop production equipment, more materials become available and more end-user industries adopt the technology.
Malaysia has been resilient amidst the impact of the COVID-19 pandemic. Additive manufacturing came in extremely handy during these times for mass customisation and production. To remain up to date and competitive in the current world economy, it is necessary for the manufacturing industry in Malaysia to adopt new frontiers of technologies such as additive manufacturing or is likely to lag behind. Major industries in Malaysia such as automotive, medical, aviation, fashion, food, and electronics have big potentials to leverage on 3D printing technologies to further innovate and expand opportunities.
Additive manufacturing uses a novel approach in manufacturing industrial parts and components. Instead of manufacturing products by subtracting the original raw materials through processes such as milling, machining, grinding, carving etc, this technology takes a different approach by depositing building materials layer upon layer in successive cross sections until the whole parts of the product is complete. In certain domains, additive manufacturing is accepted as a cost-effective production process in some of the most demanding applications. Recent efforts by system manufacturers have gone into increasing the speed of additive manufacturing machines and in automating post-processing. As additive manufacturing comes of age for production applications, it is increasing widely about applications and solutions, and less about how materials are cured, melted, jetted or bonded.
Considering that Malaysia is a global manufacturing powerhouse with various diversified subsectors, there are many existing processes that have the potential to be further improve with the use of additive manufacturing technologies. Additive manufacturing technologies is quite valuable as it can revolutionise the value chain of manufacturing industries in Malaysia. Not only does it have the potential to augment existing processes, but it can also help business operations in Malaysia to move up the value chain into a high-value business activity that will command higher profit margins. Sub-sectors within the additive manufacturing ecosystem that MIDA looks forward to nurture in Malaysia:
1. Manufacture of 3D Printers and Components
The rapid proliferation of additive manufacturing system manufacturers i.e. 3D printer manufacturers has accelerated in recent years. Generally, these 3D printers can be divided into the “industrial” 3D printer and also the “desktop” 3D printer categories. These companies spearhead the development and proliferation of additive manufacturing technologies as a total solution system.
2. Manufacture of Materials for 3D Printers
There are many different raw input materials that can be melted in building the superfine layers of additive manufacturing products but the two major categories of additive manufacturing materials by producers are polymers and metals. Thermoplastic powder and filaments remain among the most popular material as it is cheap and easily be prepared. For sturdier and more hazardous environment application, metals and metal alloys such as gold, silver, stainless steel or even titanium can be used.
Besides those main categories of additive manufacturing materials, biochemical healthcare applications include the use of hardened material from silicon, calcium phosphate and zinc to support bone structures as new bone growth occurs. A variety of ceramics including zirconia, alumina and tricalcium phosphate have also been used in Additive manufacturing.
3. Software for 3D Printer
Additive manufacturing systems have a lot in common especially in terms of the input to the Additive manufacturing systems which consists of 3D model data.
4. 3D Printing Services
An additive manufacturing service provider is a company that produces parts on additive manufacturing equipment and offers complementary services for a wide range of organizations. In recent years, the scope of paid-parts services has expanded tremendously. A service provider today may be a single individual with one desktop 3D printer selling parts locally, independent 3D print shops, Additive manufacturing marketplaces and communities, or it can even be “mega” service providers with more than 100 industrial machines with several global locations which can be called as service bureau, job shop, or contract manufacturer.
Malaysia’s additive manufacturing ecosystem still needs to be significantly improved in order to contribute more to the country’s manufacturing economy. There are two Malaysian companies engaged in additive manufacturing which are Materialise Malaysia involved in software for 3D Printing for Medical Devices and Oryx Advanced Materials which produces materials for 3D Printing.
Malaysia has a few initiatives geared toward additive manufacturing as follows: –
1. Industry4WRD: National Policy on Industry 4.0
The Industry4WRD policy is a national policy which aims to transform the manufacturing sector and related services in Malaysia through Industry 4.0 applications and technologies within the period from 2018 to 2025. Additive manufacturing has been designated as one out of the 11 Pillars of Industry 4.0 outlined under this national strategy. With this, all initiatives and incentives under the Industry4WRD policy can also be leveraged specifically to promote and encourage the adoption and development of additive manufacturing technologies within the industry.
2. 10-10 Malaysian Science, Technology, Innovation and Economy (MySTIE) Framework
This framework is a forward-thinking tool that was launched by MOSTI simultaneously together with the National Policy on Science, Technology and innovation Policy (NPSTI), 2021 – 2030. Additive manufacturing or specifically 4D/5D printing have also been identified as one of the main sciences and technology drivers under the 10-10 MySTIE Framework. 4D/5D Printing refers to printing using smart materials that change forms according to the environmental changes or responding to stimulus, and print parts as simultaneous multilayer curved layers, making the objects stronger and more cost competitive than 3D printing.
3. National Investment Aspiration (NIA)
Additive manufacturing is in line with the five (5) core parameters under the new National Investment Aspiration (NIA) such as increasing economic diversity and complexity through the development of sophisticated products and services, with high local Research and Development (R&D) and innovation, expanding and integrating domestic linkages into regional and global supply chains by improving their resiliency, and developing new and existing clusters focusing on high productivity sectors, including local products and services.
In order to remain attractive and competitive in the global market, additive manufacturing is an up-and-coming technology that Malaysia must grasp, especially for the manufacturing industry. With additive manufacturing technology, Malaysia has a strong potential for economic growth, more sustainable development and penetration of new global markets.