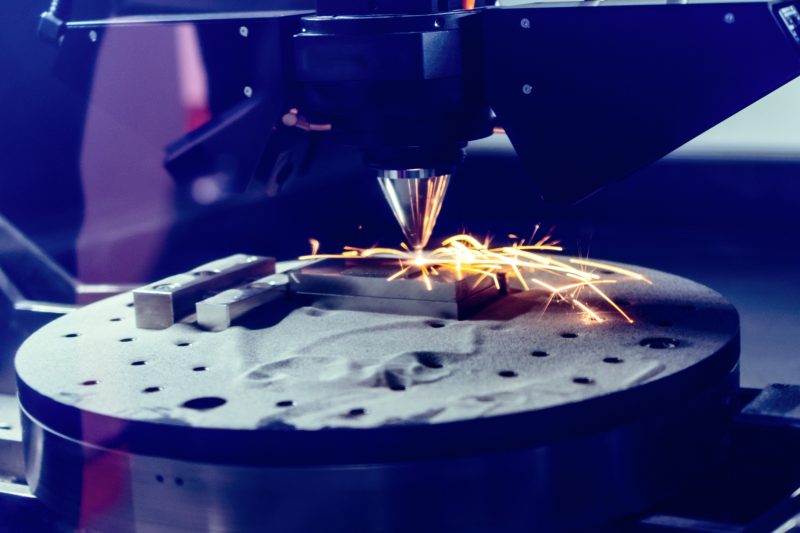
This site
is mobile
responsive
Additive manufacturing technology adds materials and melted it to create a super fine layer of an object which is different from the conservative manufacturing. Conservative manufacturing, often subtract materials via several processes such as milling, machining, grinding and carving in order to produce parts.
There are several materials that can be melted in building the superfine layers of parts.
Thermoplastic is the most popular material as it is cheap and can be easily prepared. Biochemical healthcare applications include the use of hardened material from silicon, calcium phosphate and zinc to support bone structures as new bone growth occurs. For more sturdy and hazardous environment application, metals and metal alloys such as gold, silver, stainless steel or even titanium are used.
The growth in the additive manufacturing industry is predicted by many to be rapid and substantial. As more companies develop production equipment, more materials become available and more end-user industries adopt the technology.
The findings by Frost and Sullivan suggested that the global value of the additive manufacturing is poised to grow at a compounded rate of 15% from US$5.31 billion in 2015 to US$21.50 billion in 2025. The aerospace, automotive and medical industries are expected to account for 51% of the 3D printing market by 2025.
The 2015 Wohler report stated that there have been more advances in the material production for metal printing in the past 10 years compared to plastics in the past 20 years. SmarTech Markets Publishing, through their market assessment, pointed that metal printing machines sales grew a significant amount of 89 percent over the past year, as the metal 3D printing technologies become more matured and shifted from ‘R&D’ purpose to manufacturing.
There are various technologies used in additive manufacturing such as Sintering, Direct Metal Laser Sintering (DMLS), Direct Metal Laser Melting (DMLM), Electron Beam Melting (ELBM) and Stereolithographic (SLA). DMLS uses a laser to sinter the powder across the selected surface to fuse the metal particles together. However, the metal does not melt completely. In contrast, the DMLM uses laser while ELBM uses an electron beam to completely melt each layer of metal powder. Both technologies are ideal for the manufacturing of dense, non-porous objects. SLA, on the other hand, uses photopolymerisation to print ceramic objects. The process employs a UV laser that selectively fired into a vat of photopolymer resin.
Additive manufacturing is a vital component of Industry 4.0, a key technology in manufacturing customised products. More manufacturers are beginning to see the benefits of additive manufacturing as it will reduce material wastage, provide shorter time-to-market, and able to create complex parts that are challenging to be manufactured using conventional processes. No doubt that with additive manufacturing, it becomes possible to develop an agile manufacturing environment. While additive manufacturing has been dominated by polymer and thermoplastic materials, the metal-based additive manufacturing is growing fast and provide exciting opportunities and possibilities, not only in the design but also in the choice of materials for the end products.
As at today, based on MIDA’s record there is only one company producing metal powders for 3D printers namely Oryx Advanced Materials in Malaysia, and so far, there are no companies producing 3D printers for metal applications. Oryx Advanced Materials is one of the leading metal and alloy producers for hard disk drives and photovoltaic modules. They are expanding their products portfolio by including metal powders for additive manufacturing. Their facility in Penang provides total solutions for metal additives manufacturing from material characterisation & selection, 3D printing services and post-processing processes. Realising the importance of additive manufacturing as one of the disruptors in the manufacturing industry, MIDA with Oryx had co-organised a one day workshop on metal additive manufacturing in Penang on 10th April 2019. The one-day event featured speakers from EOS, Materialise, Oryx and MIDA. The workshop covered a broad spectrum of additive manufacturing from services, manufacturing up to the angle of policymakers. During the event, Mr. Zabidi Mahbar, the Deputy CEO of MIDA in his keynote address highlighted that additive manufacturing will change the ways of doing business and it will require comprehensive collaboration from all stakeholders to drive the country’s digital transformation agenda. Oryx also organised an open factory event in the evening to share their capabilities with the seminar participants.
Initiatives by the Government
The National Policy on Industry4WRD was launched on 31 October 2018 to drive the country’s growth and transformation via digitalisation. Additive manufacturing has been identified by the Government as one of the technology elements under the Industry4WRD.
Related industry players who wish to adopt additive manufacturing technology can utilise the Readiness Assessment (RA) or Domestic Investment-Specific Fund (DISF) facilities provided under the Industry4WRD. The RA will assist the company in providing a full diagnostic report for their readiness level before adopting the additive manufacturing technology.
The report will identify the gaps, areas of improvement as well as recommending realistic framework and strategies for companies in adopting the technology.Companies can also apply the Industry4WRD DISF if they require monetary assistance in implementing the strategies for adopting additive manufacturing in the manufacturing line.
For companies who would like to automate their production line, the Government has also announced an Automation Capital Allowance (ACA) in 2015.This is one of the Government’s initiatives to further encourage quick adoption of automation especially for industries that are heavily reliant on foreign workers.
The metal additive manufacturing technology is rapidly evolving and disrupting the whole manufacturing value chain. Like many new technologies, early adopters often race ahead and garner early returns.