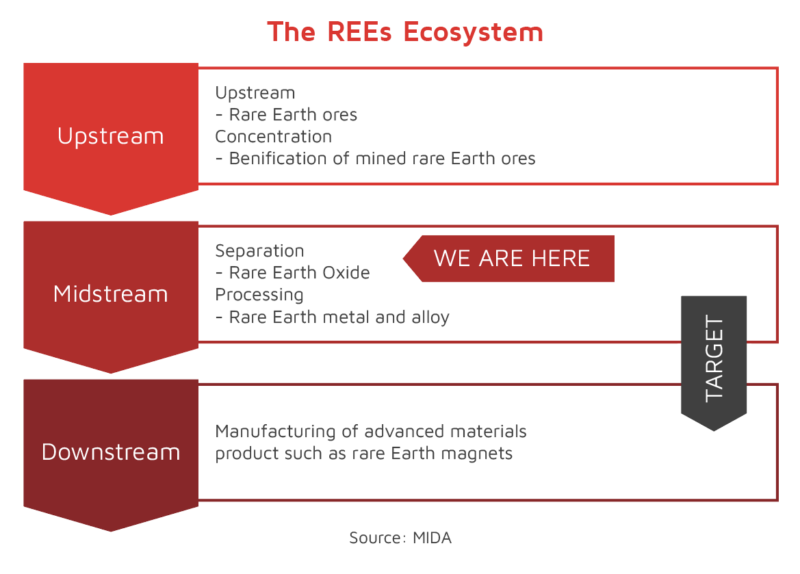
This site
is mobile
responsive
For the past decade, rare earth elements (REEs) have soared in significance as interest in consumer electronics, electric vehicles, clean energy, and military equipment keep on increasing. To achieve growth in advanced technology, the development of REEs as a strategic mineral modern society.
REEs are used as a necessary component for products across a wide range of applications, especially high-tech consumer products and devices, including smart phones, digital cameras, computer hard disks, fluorescent and light-emitting-diode (LED), flat screen televisions, computer monitors, and electronic displays.
In terms of military equipment application, REEs are materials included in night vision goggles, precision guided weapons, communication equipment, Global Positioning System (GPS) equipment and other defence electronics. REEs are also used for laser targeting and weapons in combat vehicles.
Additionally, REEs are also known for their usage in clean energy technologies – for example wind turbines, electric motors, catalysts and solar panels due to their strong permanent magnetic properties. As for electric vehicles, mainly two types of REEs are used; neodymium (Nd) and dysprosium (Dy). Nd is used in permanent magnet motors, which are often termed as neodymium iron boron magnets. Dy is also used in motors but in minimal amounts relative to Nd.
The strength of rare-earth magnets
One of the strongest types of permanent magnets is the rare-earth magnets made from alloys of REEs. There are two (2) types of rare-earth magnets, neodymium magnets and samarium–cobalt magnets. Both materials come in different grades of strength and have different magnetic and physical properties.
Neodymium magnets, the stronger of the two, are composed of alloys made primarily of neodymium, iron and boron. However, neodymium magnets are incredibly brittle and vulnerable to corrosion and hence they are usually nickel-plated or coated to prevent breaking, chipping, or crumbling into powder. Samarium cobalt magnets are made primarily from alloys of samarium, cobalt and iron. These magnets have moderately high operating temperatures and a strong resistance to corrosion.
Common applications of such magnets include computer hard disk drives, wind turbine generators, speakers and headphones, bicycle dynamos, magnetic resonance imaging (MRI) scanners, traction motors and integrated starter-generators in hybrid and electric vehicles.
Neodymium is considered to have the world’s mightiest magnetic powers, making it essential for missile guidance systems. Lanthanum enhances the clarity of glass, particularly for high-end camera lenses, used for intelligence, surveillance, and reconnaissance missions. Phosphorescent europium warms the hues in LED lights and plasma displays, with its unique neutron-absorbing properties making it a crucial ingredient in control rods used in nuclear reactors.
Potential of rare earth materials production in Malaysia
Today, the People’s Republic of China (PRC), boasts from having the largest reserves of REEs at 44 million tonnes in addition to having the largest refinery controlling the market. Malaysia was able to break that monopoly with the presence of Lynas Malaysia Sdn. Bhd. (Lynas), whose operation locally since 2012 made it the first REEs refining plant outside the PRC. Malaysia is also recognised as a nation having notable production of REEs materials, among other countries such as the US, Australia, Brazil, India, Russia, Thailand, and Vietnam.
It must be noted that Japan has one of the best material sciences industries in the world, alongside being one of the top countries to produce materials such as magnets, catalysts, and electronic components. After years of suffering from a lack of steady supply for REEs, Japan has now been able to source the materials from Malaysia – which has enabled Japan to recover and increase their activities since 2013.
REEs ecosystem and opportunities for Malaysia
The REEs ecosystem is basically divided into three (3) main streams: upstream, midstream and downstream. The basic ecosystem is defined as in chart below:
Currently, Lynas produces rare-earth oxides, carbonates, oxalates and chlorides in Gebeng, Pahang, with a total capacity of 22,000 tonnes per annum. The production of rare-earth oxides (REO) – particularly Nd and praseodymium (Pr), are highly in demand to produce rare-earth magnets that will be used in technological applications.
The global rare-earth magnet market was valued at US$7.69 billion in 2020, and it is expected to reach US$11.61 billion by the end of 2026, representing a compound annual growth rate (CAGR) of six (6) per cent from 2022-2026.
Recognising the potential of this downstream industry as well as the advantages of having REO production as raw materials in the country, the Government, through the Malaysian Investment Development Authority (MIDA), has been promoting the production of advanced materials including rare-earth magnets under the Promotion of Investment Act (PIA) 1986.
There is high potential for interested parties – either local or foreign companies to explore downstream applications to boost the industry’s economic value. Additionally, establishing a downstream ecosystem will ensure more value-added products are produced in the country, which will directly impact the total export status of Malaysia.
As such, it must be stated that the value of REEs as an important element in the downstream industry value chain should not be ignored, and that its ability to leave a mark on the nation’s future technological journey should be acknowledged.
To continuously support this, MIDA will continue its collaborations with the relevant stakeholders to attract potential investors to develop the industry. The support will focus on downstream manufacturing activities, as well as integrated projects including rare-earth metals manufacturing that can convert oxides into metals. It is for these reasons that MIDA encourages potential investors to explore the business prospects of the REEs ecosystem.
For more information, please contact MIDA’s Chemical and Advanced Materials Division.
Newsletter February 2022