Speedier hiring good but automation still important
16 Jan 2023
Hastening the inflow of foreign labour to ease the manpower shortage could potentially bolster gross domestic product growth by as much as one percentage point for the first quarter of 2023, Home Minister Datuk Seri Saifuddin Nasution Ismail said in a statement dated Jan 5, as he pledged to shorten the processing period of hiring migrant workers to less than 30 days.
The potential boost mentioned, if delivered, would prove helpful, given that economic growth is projected to slow to between 4% and 5% this year from around 8% levels in 2022.
In the longer term, however, policy measures need to be stepped up to ensure that the country can cut its reliance on low-skilled and low-wage foreign workers and move to higher productivity and value-added processes with higher-paying jobs for locals. As it is, Malaysia’s robot density per 10,000 employees — an indicator of automation adoption in the industrial/manufacturing industry — is not only way below the global average, but also behind that of neighbouring Thailand. More on this later.
In the near term, the onus to deliver an end to labour shortage issues is on the Ministry of Home Affairs (MoHA), which would be taking charge as the “main custodian” for the management of foreign workers, while the Ministry of Human Resources (MoHR) continues to take care of compliance on labour policies, quota eligibility and cooperation with source countries.
Noting that “three-quarters of the approval and application process would be under the MoHA”, the Malaysian Employers Federation (MEF) — which prefers having a single recruitment centre under MoHR but “accepts” the cabinet’s decision — hopes in its Jan 6 statement that “the processes to bring in foreign employees will be more efficient and smoother without any delays and the related high costs”.
“When such a policy [to reduce processing time] is in place, employers can [heave] a huge [sigh of] relief that the shortage for foreign employees faced by businesses for the last three years will finally be over,” the MEF’s statement reads.
“Efforts to quickly fill the gap for foreign employee shortages will assist the nation to be more competitive and improve its ranking in the IMD Competitiveness Index, where Malaysia was at 32 out of 64 countries in 2022,” MEF president Datuk Syed Hussain Syed Husman says in the statement.
Tan Sri Soh Thian Lai, president of the Federation of Malaysian Manufacturers (FMM), in a separate statement dated Jan 6, also welcomed a speedier recruitment process and expressed preference for “one level of approval” by a single handling agency for the entire foreign worker employment process via a single online system “with no carve-outs of processing to third-party service providers and no cost to employers when accessing/using the system, which is the current practice via the Foreign Worker Centralised Management System (FWCMS)”.
Having one system and a single agency for employers to deal with also means issues can be resolved faster, ensures that only a single central repository of foreign worker database is maintained and removes discretionary powers of officers to approve applications, the FMM says. “Given that the changes would come into effect from Jan 15, 2023, the industry seeks engagement with the ministries concerned to better understand the latest announcement and ensure a smooth transition arising from this realignment of functions,” the FMM adds.
If indeed the cabinet’s decision is intended to drive better economic growth for the country in 2023 by ending the long-drawn labour shortage issues faced, employers and industries should be looking at better days ahead.
In any case, business owners and industries may want to explore avenues in automation and robotics that can help reduce their dependence on foreign workers in the future.
Malaysia Robotic Roadmap 2030
Many may not know that under the “Malaysia Robotic Roadmap 2021 to 2030”, the country aims to not only become a high-tech nation by 2030 but also be a regional robotics hub in services, agriculture and manufacturing. The roadmap sees Malaysia’s robotics market worth US$88.46 million in 2020 growing at a 17.5% compound annual growth rate (CAGR) to US$273.61 million by 2027, “with strong support towards automation and IR 4.0”. It also expects the country to produce 4,742 units of robots by 2027 or a 16.77% CAGR from 2020.
More importantly, under the roadmap, Malaysia aims to utilise technology to increase labour productivity growth from the current 1.8% per annum to 3.6% per annum, which is the average for developed countries, by 2030 — less than seven years away.
Citing a study by the Centre for Economic Performance at the London School of Economics in 2018, the roadmap notes that every one unit increase in robot density will contribute to a 0.36% increase in labour productivity. With a forecast of around three unit increases in robot density every year, robotics is estimated to boost labour productivity by around 1.08 every year, the roadmap says.
The roadmap admits this, though: “While robotics technology has substantial benefits to the country’s market growth, the high cost of acquisition, as well as maintenance of the technology, has restrained most of the industries in Malaysia from adopting and utilising robotics technologies in their industry.
“In short, industries have to spend significantly not only to acquire the robots but also to maintain them. The prohibitive costs of acquiring both robotic components and technologies have resulted in minimal robotics development and commercialisation at the local level with locally developed robotic products rendered uncompetitive in terms of price and support available.”
Even so, a “concerted, strategic approach and robust intervention should be taken towards enabling and increasing robotics adoption in local industries” for the country to at least reach global average by 2030, given that the deployment of robots in manufacturing and other economic sectors “would certainly offer tremendous benefits to the industry, including optimisation of operations, time efficiency, accuracy and productivity”, the roadmap reads.
Among other things, the roadmap notes that awareness should be raised among industry players that there are incentives — be it tax benefits, grants or lease facilities — that could support robotics adoption such as the automation incentive provided by the Malaysian Investment Development Authority (MIDA) as well as the domestic investment strategic fund, the Industry4WD intervention fund and the Smart Automation Grant (SAG). Project implementation could then be expedited by leveraging the Project Acceleration and Coordination Unit (PACU).
Under the roadmap, Malaysia aims to raise robot density per 10,000 employees in manufacturing from just 55 units per 10,000 employees in 2019 to 195 units per 10,000 employees by 2030, the expected global average. This can only be achieved with policy intervention, without which robot density is expected to only reach 67 per 10,000 workers in 2025 and 82 per 10,000 workers in 2030 — 137.5% shy of target.
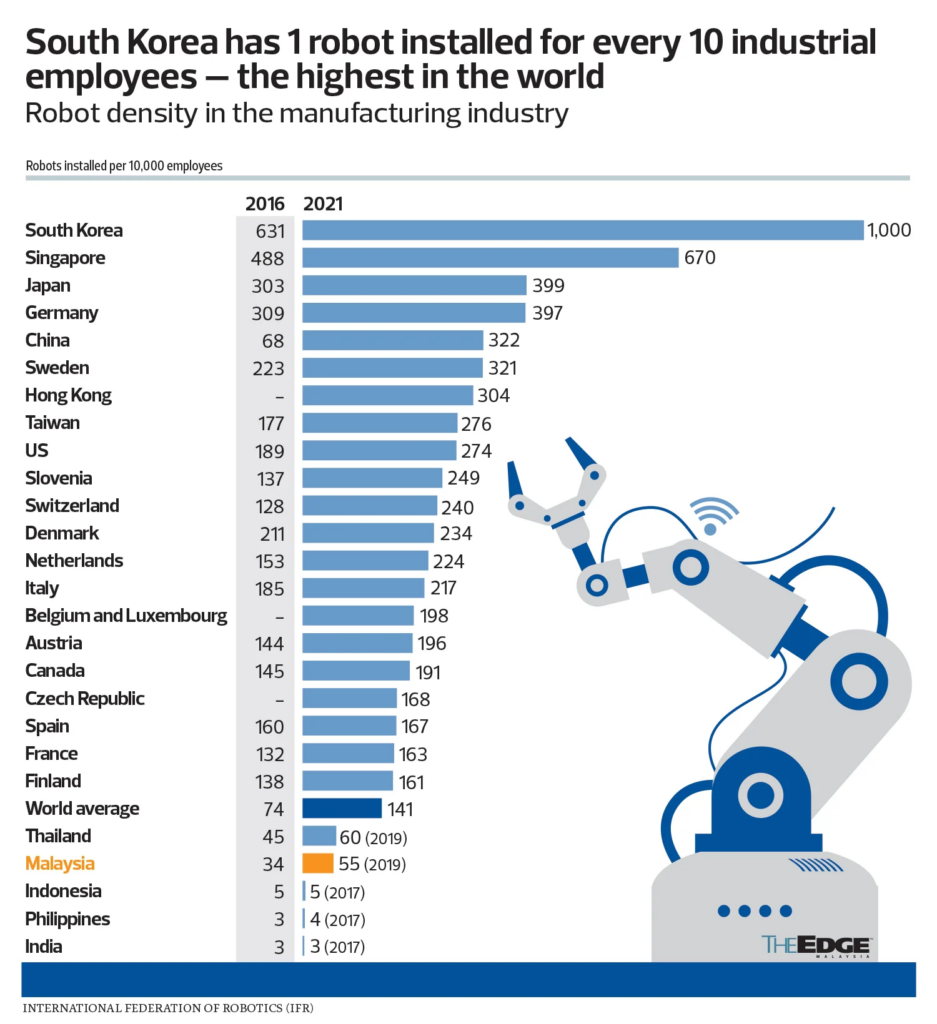
At 55 robots per 10,000 employees in 2019, Malaysia was behind Thailand, which had 60 robots per 10,000 employees. Thailand was already ahead of Malaysia in terms of robot density in manufacturing in 2016, according to data from the International Federation of Robotics (IFR) (see line chart).
Back in 2019, the world average was 113 robots per 10,000 employees and this rose to 141 robots per 10,000 employees in 2021, IFR data shows. Data for Malaysia and Thailand for 2021 is not immediately known.
China’s rise
Policymakers here may want to take a leaf out of global leaders’ book, including China, which had an outsized workforce and only 68 robots per 10,000 industrial workers back in 2016 (when South Korea had 631 and the US had 139) but had aimed to more than double that to 150 per 10,000 employees by 2020 — a target that the country exceeded by 2019, IFR data shows.
China’s “massive investment in industrial robotics has put the country in the top ranking of robot density, surpassing the US for the first time” in 2021, according to the IFR’s statement dated Dec 5, 2022.
China — with 322 units of operational industrial robots for 10,000 employees in the manufacturing industry — is ranked the fifth most automated country in manufacturing in 2021, behind South Korea, Singapore, Japan and Germany (see bar chart).
“Robot density is a key indicator of automation adoption in the manufacturing industry around the world,” Marina Bill, president of the IFR, says in the statement, noting that the new average of global robot density in the manufacturing industry surged to 141 robots per 10,000 employees — more than double the number six years ago.
“China’s rapid growth shows the power of its investment so far, but it still has much opportunity to automate,” she adds.
According to the IFR, China is “by far the fastest-growing robot market in the world”, has the highest number of annual installations and, since 2016, has had the largest operational stock of robots. Japan has also seen its robot density grow 6% on average every year since 2016 while Singapore’s robot density had grown by 24% on average during the same period.
The global leader is South Korea, which now has 1,000 industrial robots per 10,000 employees — or one for every 10 — in 2021, three times that of China’s. “With its globally recognised electronics industry and a distinct automotive sector, the South Korean economy profits from two large customer industries for industrial robots,” the IFR notes.
Among the leading countries, IFR data shows that most of these robots are installed in the semiconductor, electrical and electronics, automotive parts, motor vehicle, metal and machinery sectors. These are all areas in which Malaysia needs to step up its game to remain competitive in the global supply chain in the long haul.
According to the roadmap, only a small group of home-grown producers are producing robotics components and materials while the majority are system integrators, solution providers and product distributors.
“Currently, Malaysia’s robotics strength lies in system integrators where most of its leading robotics firms such as Pentamaster and ViTrox have contributed to the industry’s progress. For Malaysia to become a regional robotics hub in services, agriculture and manufacturing by 2030, it must focus on promoting home-grown essential components for robotics, materials for the development of the robots and eventually home-grown robots. A strategic approach to mergers and acquisitions between the high-potential global robotics enterprises and local robotics enterprises/unicorn companies can be implemented for the gradual development of local capacity and capabilities. In the long term, these robotics components can be assembled together to produce fully home-grown robots,” the roadmap says.
The roadmap rightly points out that there is a need for Malaysia to facilitate locally produced robotics components and materials. That much is clear looking at how global leaders are able to bring down the cost of adoption. Indeed, the gap here is not just the high cost of sourcing technology from overseas, but also the absence of locally produced robotic components as well as professional service and certifications to support local development and commercialisation. There is much catching up to do.
Source: The Edge Markets